DIY Boatyard: Builds from Scratch, plus Sprucing up America’s Cup USA 76
DIY Boatyard and Building Rediviva
What reader here has not clicked through Instagram travel photo feeds? And who has not paused to read about how one sailor or another solved an onboard plumbing issue, or brought a gleam back to 50-year old brightwork? Cruisers, racers and DIYers love to show and tell, but some of the best stories come from those who build a boat from scratch.
Meet Ruth and Garrett Jolly, a twenty-something couple who share via their YouTube channel Salt & Tar and blog saltandtar.org. This duo planned on building a 42-footer but settled on something a bit more manageable, and it all started with a wee bit of lofting in 2015, in Washington state, in a shed.
Ruth smiles, “It’s a Buehler design called Button. We loved the salty lines of the Button’s hull, but the deck, cabin and rig were not right for us. Luckily George Buehler is awesome and has done a bunch of custom work on the plans so she will be exactly what we want. She will be a 35-foot gaff rigged ketch, complete with rat lines, baggy wrinkles and top mast. Wildly impractical, but dreams aren’t always practical, so salty she will be!”
Background on the DIY
First, a little background about this pair who met on the islands in their mid-teens. It was serendipity that each family happened to vacation in Aruba each year. And it was serendipity each family happened to live in California—a mere five hours apart. But it was a casual conversation between two mothers (while standing in the hotel shuttle line) that clinched a connection—leading to a pairing that’s outlasted a family holiday. Happily, both Ruth and Garrett enjoy building boats and neither is a stranger to planks or pliers.
Over the years this couple has restored a 40-foot mahogany racing boat, and has toiled on a 30-foot wooden ketch in need of plenty frame work; they also copper-plated the bottom of that ketch. Garrett, who started sailing at age seven, has worked on boats since age 15, and in the past six years has completed six major boat projects. Ruth admits to having no sailing experience prior to meeting him.
“He was building his first sailboat, a 20-foot Vacationer, in his mom’s backyard. We bought our first boat together just two days after I turned 18, then sailed from Santa Barbara to Port San Luis, around Point Conception.” Revealing, “Prior to Rediviva, we’d travel most of the year then stop and find work when the kitty ran low.”
This DIY boatyard duo planned on building a 42-footer but settled on something a bit more manageable. The build of their DIY boatyard gaff rigged ketch initiated in Washington. After toiling outdoors through two brutal winters, they transported the project south. “We had four and a half feet of snow up there, and often saw single-digit temperatures,” Ruth states. “Plus, we have family in Napa and around the Bay Area.” Since fall the duo has been tucked in a corner of the Napa boatyard, working tasks such as caulking the hull, priming/painting, installing the prop shaft, making the hardware to hang the rudder and installing the rudder.
At the end of March a most trialing task was undertaken: extracting the rudder which is made out of old growth fir and is two layers of 2 × 10s sandwiched together. Notes Ruth, “Height of the rudder is as tall as the boat since it will hang off the back, and the tiller will come over the transom. To get it into the boat for transport we had to lift it up, just the two of us, probably 15 feet on rickety scaffolding to reach the deck. Then down into the boat, which doesn’t yet have companionway stairs, and over the engine to be secured inside.”
Fortunately, Garrett’s brother Reid arrived just as the lift-up started. Overall things are going great, reports Ruth. Both are optimistic that splash time will occur in late summer, to be followed by rigging, interior and finish work.
DIY Boatyard and the Persistent Duo
The duo perseveres, but building Rediviva has been a huge challenge; the physical and mental tolls are tough. Shares Garrett, “I knew that I didn’t want to take forever to finish, so I set out to get thing done as quickly as possible for my DIY boatyard project. After two years of full time hard labor I’m not quite as nimble as I once was. Looking back, it makes more sense to slow down a bit and make time for yourself even when trying to accomplish such a big goal.”
Ruth adds, “At the start of any project you try and weigh the pros and cons, the probable failures and successes, and the troubles it will take, but truth is you’ll never be fully prepared. I failed to think about the stress on our relationship. When thinking about the project we’d talk nuts and bolts, not feelings. This project has taken everything we have—including our energy, sanity and above all patience.” Nonetheless, she reveals they have learned so much.
“Not only about boats, but also about life, about patience, perspective, and how to love and support each other more deeply. It’s shown both of us what we can accomplish if we just go for it, As long as we have each other we can overcome the various obstacles along the way.”
Continuing, she says, “Napa boatyard has always been really great to us. They definitely had their reservations at first, and rightfully so, when a pair of 20 year olds decide to haul-out an old 40-foot wooden sloop. But we got it done, and have always welcomed us back to do DIY boatyard tasks. The atmosphere here is really laid back, and the yard is full of cool and interesting people. It is one of the last do-it-yourself boatyards where individuals can work on their own boats. I’m not too sure of many other yards that would let in a project like ours.”
The plan is to sea-trial the boat in the San Francisco Bay to work out kinks. Smiles Garrett. “Our intention is to live on the boat and travel as far as we feel like going. We stopped making plans a long time ago. Now we just make ideas, because plans always seem to be over-ruled by spontaneity.”
USA 76 will be age 16 this July
She embarked on her 1000th trip May 6, 2017, and has shared the America’s Cup experience with more than 16,000 fans. She adds a signature touch to San Francisco Bay, and we’re working hard to keep her on the water for years to come,” says Brad Webb who, along with wife Karen, founded and operate ACsailingSF.
This beauty receives a haul-out at the start of every year to ensure readiness for the upcoming season. “We work with KKMI’s schedule to work over a long weekend. This timing allows the boat to remain in the travel lift and avoid going into the cradle. KKMI is the only deep water marine facility in San Francisco (USA 76 draft is 14 feet), and we’ve had a great relationship with Paul and his team since our USCG refit in 2011.”The crew sail her north the night prior, then initiate prep. “To haul, we use a beam and center-point lift rather than a sling (which requires rods, strops, shackles and stabilizing lines).
It’s important to make sure everything is properly installed and loaded carefully; she weighs 50,000lbs—40,000lbs of that is in the bulb.” Once out of the water, the yard crew power-wash below the waterline, then find a level spot to rest her down. “As soon as she is set on the bulb cradle, we inspect all underwater surfaces and connections to check for any issues.”Back in January, the first action item was to remove the rudder and rudder bearing, plus propeller and sail drive. Shares Webb, “The rudder bearing is a custom design and machined assembly from JP3 in France, so we take particularly good care of this hardware. The Gori blade and Yanmar SD 50 are also key components and receive close attention.” While those tasks are being handled, a pair of KKMI team members worked from a scissor lift to sand the hull and keel to remove loose paint and key the surface.
On day two, the rudder bearing and sail drive were disassembled, cleaned and inspected; any worn components were replaced. The outer surfaces received a new layer of anti-corrosion spray before being rebuilt and reinstalled. The keel root was stripped back, inspected and dye tested, then protected with four coats of epoxy primer. “This application lasts a full year, however we generally start sending a diver down on a monthly basis around month four to clean the waterline and replace anodes. If there’s time, a few above-waterline jobs get done, but the priority is the bottom. We need at least four crew per day to meet the timeline. This year Jon, Peter and Brad were on deck throughout dry dock time, with several of our regular crew putting in one or two nine to ten hour days.”
USA 76 Celebrates a Sweet 16 at her DIY Boatyard
The number of tasks to do during the routine three-day haul-out is lessened since the crew follows strict maintenance and care procedures year round. “Some of these standards are USCG mandated, but many are self-imposed to our own high standards,” says Webb. “Sails and winches require the most attention throughout the season. We teach our crew how to maintain the drive train and make minor repairs to the main and jib. We keep on top of the small jobs to keep the boat constantly looking authentic, clean and safe.”
“USA 76 is a unique boat, the most modern America’s Cup yacht in the world available for charter. Considering that, and summer conditions on the San Francisco City Front, we take the responsibility of maintaining and operating her very seriously.” Hence, a DIY boatyard annual trip is routine. Did you know that USA 76 participates in Friday night racing at South Beach YC in San Francisco? Join the fun: https://www.acsailingsf.com/americas-cup-racing
Much of what was learned in composite structural engineering and applied to USA 76 is still applicable today. The most obvious development is the leap to foiling and the flight systems required
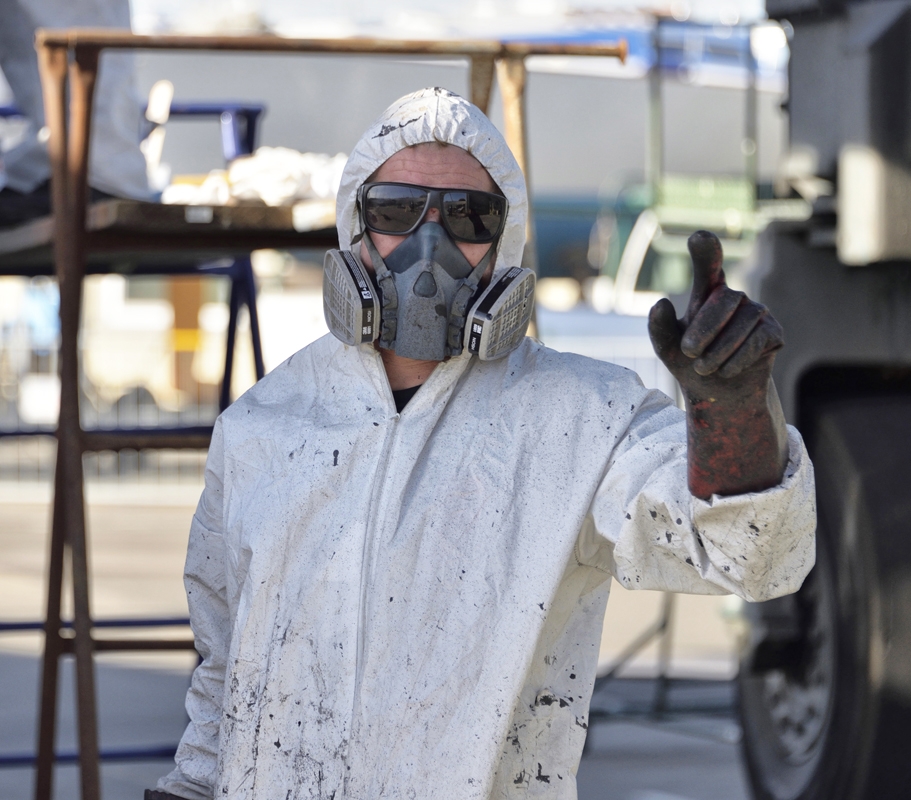